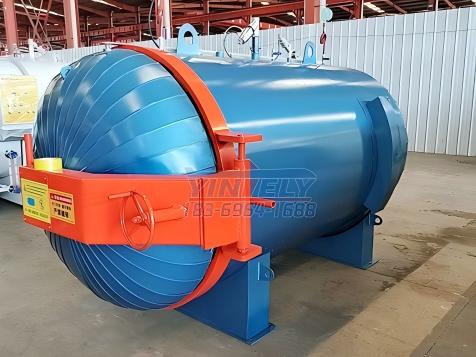
電干燒硫化罐的工作原理
電干燒硫化罐是一種通過電加熱元件實現(xiàn)高溫高壓環(huán)境,,促使橡膠,、塑料等高分子材料發(fā)生硫化交聯(lián)反應的工業(yè)設備,廣泛應用于輪胎制造,、密封件加工,、復合材料固化等領域。
其核心功能是通過精準控制溫度,、壓力和時間,,將線性分子鏈結構轉化為三維網(wǎng)狀結構,從而提升材料的強度,、彈性和耐候性等物理機械性能,。
設備的核心構造圍繞高效加熱與精準控壓展開,主要包括罐體,、電加熱系統(tǒng),、加壓裝置與智能控制系統(tǒng)等關鍵部分。
罐體作為承載主體,,采用高強度鋼材制成圓柱形壓力容器,,內壁通常進行防腐處理以適應硫化環(huán)境,罐門設計為快開式結構并配備高密封性橡膠圈,,確保在 0.3~1.0MPa 壓力和 120~200℃高溫下無泄漏,。
電加熱系統(tǒng)分為直接加熱與間接加熱兩種模式:直接加熱通過內置電阻絲或電加熱管直接輻射加熱,適合小型設備快速升溫,;間接加熱則借助導熱油或空氣循環(huán),,通過外置加熱爐或內置風道式加熱器傳遞熱量,配合風機強制對流,,實現(xiàn) ±1~2℃的高精度溫控,,滿足大型罐體或精密制品的硫化需求。
加壓系統(tǒng)與加熱系統(tǒng)協(xié)同工作,,通過空壓機向罐內注入壓縮空氣,,形成與溫度匹配的壓力環(huán)境。
壓力的作用不僅在于確保制品與模具緊密貼合,、避免氣泡缺陷,,更能加速分子交聯(lián)反應,提升材料致密性,。
部分設備還支持電 - 氣混合模式,,引入蒸汽輔助加熱以調節(jié)濕度,適應特殊工藝要求,。
控制系統(tǒng)作為設備的 “大腦”,,由 PLC 或工業(yè)計算機集成溫度、壓力傳感器數(shù)據(jù),,按照預設的硫化工藝曲線(如升溫速率,、保溫時間、壓力梯度)自動調節(jié)加熱功率和氣體流量,,人機界面實時顯示運行參數(shù)并提供故障報警功能,,例如超溫時自動切斷電源、壓力未泄放時鎖定罐門等安全聯(lián)鎖機制,,從根源上杜絕操作風險,。
硫化過程遵循嚴格的工藝邏輯:
首先將模具與坯料裝入罐內,鎖緊罐門后啟動電加熱元件,以 5~10℃/min 的速率升溫,,同時通入初始壓力防止制品變形,;
達到目標溫度(如 150℃)和壓力(如 0.6MPa)后進入保溫保壓階段,持續(xù)時間根據(jù)材料厚度和配方調整,,確保交聯(lián)反應充分進行,;
完成后關閉熱源,通過水冷或風冷系統(tǒng)降溫,,待溫度降至 60℃以下再緩慢泄壓,,避免驟冷驟壓導致制品開裂;
最后開啟罐門卸料,,清理設備進入下一循環(huán),。
與傳統(tǒng)蒸汽硫化罐相比,,電干燒硫化罐具有顯著的技術優(yōu)勢,。
其電能轉化效率高達 90%,無需等待蒸汽預熱,,即開即熱且無管道熱損耗,,配合 PID 智能控制實現(xiàn)精準溫控,尤其適合多品種,、小批量生產(chǎn)場景,。
同時,電加熱模式無廢氣排放,,避免了蒸汽系統(tǒng)的冷凝水處理問題,,符合現(xiàn)代工業(yè)環(huán)保要求。設備設計兼顧靈活性與兼容性,,支持多段工藝曲線編程,,可滿足輪胎、密封圈,、航空復合材料等不同制品的個性化硫化需求,。
在安全維護方面,需定期校驗壓力表,、安全閥等承壓部件,,每年進行罐體無損檢測,確保壓力容器安全,。
日常保養(yǎng)包括清潔加熱元件表面積塵,、潤滑罐門啟閉機構、檢查密封圈磨損情況,,避免因部件老化引發(fā)泄漏或加熱失效,。
對于使用易燃硫化劑的場景,,還需額外配置防爆裝置和通風系統(tǒng),從設備本質上保障生產(chǎn)安全,。
典型應用中,,轎車輪胎的胎體硫化通過電加熱罐的梯度升溫工藝,有效消除內外溫差導致的內應力,,提升胎面耐磨性,;
精密橡膠密封圈采用強制對流加熱,,確保薄壁制品硫化均勻,,避免缺膠或過硫缺陷;
航空航天領域的碳纖維樹脂基復合材料,,則依賴其高精度溫控功能,,嚴格控制樹脂流動速率,防止層間缺陷,,保障結構件力學性能,。
作為綠色制造的重要裝備,電干燒硫化罐正朝著節(jié)能化與智能化方向發(fā)展,。
電磁感應加熱技術的引入進一步提升熱效率,,物聯(lián)網(wǎng)模塊實現(xiàn)遠程監(jiān)控與數(shù)據(jù)追溯,使其不僅是單一加工設備,,更成為工業(yè) 4.0 體系中可實時交互的智能節(jié)點,。
隨著高分子材料應用的不斷拓展,這類設備將以其精準,、高效,、環(huán)保的特性,持續(xù)推動橡膠與復合材料加工行業(yè)的技術升級,。